Managing Risk in the Global Supply Chain, a report by the supply chain management faculty at The University of Tennessee, ranks natural disasters as the third biggest supply chain risk, following quality problems and the need for increased inventory due to longer supply chains.
The March 11, 2011 natural disaster in Japan brought to light the fragile nature of the global supply chain. Professor Willy Shih discussed how companies should be rethinking their supply chain strategy in response to this risk.
Very little has appeared to change in the five years following.
According to the study, 90% of firms do not formally quantify risk when sourcing production. Most firms, 54%, consider unit cost, transportation and inventory, while 36% of them consider only unit cost and transportation.
“Manufacturers have spent years building low-cost global supply chains. Natural disasters are showing them just how delicate those networks really are,” Bill Powell argued in a 2011 article for Fortune.
Natural disasters such as the Japan earthquake and tsunami in 2011 reveal just how quickly this carefully crafted ecosystem can be dramatically disrupted.
As Bob Ferrari, a leading supply-chain consultant, puts it:
You never want to hear about the guys who run the supply chains for multinational companies. When you do, usually it means something really bad has happened.
The need for better warning recognized at the top
The White House recently held an Earthquake Resiliency Summit, which brought Interior Secretary Sally Jewell together with the USA’s best seismologists.
Spurred on by new fears that the “Big One” will soon be rattling the West Coast, the administration proposed stronger efforts to prepare for earthquake-related devastation.
“We have the real opportunity to mitigate damage and save lives if we act now on an early warning system,” said summit participant Rep. Adam Schiff, D-Calif.
“Seismologists and other experts say that, in theory, early notification of an impending quake – even if it’s just a few seconds – would help. Transit systems could slow trains; pipelines could be closed off; first responders could be alerted; power could be rerouted; other public sector utilities could be warned as well.”
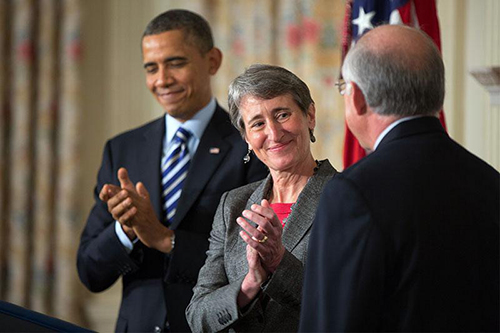
How common are quakes around the world? The USGS said there were 14,588 earthquakes of magnitude 4.0 or greater throughout the world in 2015; California has scores of quakes every week, but most are not strong enough to be felt by residents.
As you might expect, California tops the list of states most at risk, but states in the eastern United States have a greater chance of having a damaging quake than was previously thought.
A lot was learned from the magnitude-5.8 earthquake that hit Virginia in 2011, researchers say; the quake caused considerable damage and forced the Washington Monument to close for repairs, which were just completed in May 2014.
There are other parts of the U.S. where the “Big One” could strike. The New Madrid Fault Line zone in the central United States also has more potential for a larger quake than previous estimates suggested.
The zone could have a devastating earthquake that would be felt in nearly a dozen states, researchers say, threatening large cities such as St. Louis, Memphis, Nashville and Atlanta.
The recent catastrophes in Japan, Nepal and New Zealand show that the threat of devastating earthquakes remains a worldwide problem.
Until recently, the mitigation of the effects of earthquakes did not occupy a high priority in discussions of supply chain disruption. One of the reasons for that is the fact that earthquakes are so different from other natural hazards.
They cannot be predicted, and when they occur the warning time, even with an early warning system in place and operating, is measured in seconds – typically 15-20 seconds, depending on the distance from the epicenter.
That is a vastly different scenario than other disasters such as floods, hurricanes, tornados, wildfires and even tsunamis.
How does earthquake early warning work?
When an earthquake occurs, it begins in one location and the energy that is released radiates out in all directions, causing the ground to shake in the surrounding areas.
Sensors in place throughout the region detect the initial earthquake and radiating waves of energy to predict where the shaking will go, how strong it will be, and how long it will take to reach various locations.
This information is then used to rapidly send out a warning, giving the recipients anywhere from seconds to minutes to take protective actions. The farther from the initial earthquake a location is, the more warning time they can receive.
What actions can I take in those extra seconds?
While a few seconds to minutes doesn’t seem like much warning time, even a few seconds of warning can enable protective actions such as:
- The ability of individuals to drop, cover, and hold on, turn off stoves or safely stop vehicles.
- In the workplace, personnel can move to a safe location, automated systems can ensure elevators doors open, production lines may be shut down and sensitive equipment placed in a safe mode.
- Surgeons, dentists, and others can stop delicate procedures.
- Emergency responders can open firehouse doors, personnel can prepare and prioritize response decisions.
- Power infrastructure can protect power stations and grid facilities from strong shaking.
What automated controls should be put in place?
Automation is needed to take maximum advantage of what may be only a few seconds of warning time.
- Warning appliances should interface with factory, building and process automation systems. Legacy warning systems like the Emergency Broadcast System are too slow for automated earthquake warnings. Communications should and can take less than a second to avoid wasting precious time.
- Communications to automated controls should be encrypted to prevent unauthorized access or terrorist accesses to sensitive infrastructure.
- Communications security is essential when using earthquake warning to automatically protect property or controls on transportations systems.
Preventing dangerous false alarms
If people don’t trust the warning they won’t respond immediately. False alarms must be absent.
- A false alarm in a nuclear facility transportation system or refinery can have extremely undesirable consequences, including incurring large costs associated with complex restart procedures and losses of revenue due to being offline, not to mention resultant impacts from service interruption, affecting downstream customers.
- Unlike all other natural disaster warnings, there is no timely way to confirm an earthquake warning. There must be an immediate response.
Training and education is crucial
People must be trained to respond immediately to the warning. Seconds count, and there may be little time before the damaging shaking begins.
All earthquake warning fundamentally relies on quickly and accurately detecting an earthquake, and then successfully sending a warning out to people and/or automated devices to trigger appropriate actions before the shaking begins.
But if the proper knowledge and training isn’t in place, prompting the correct reactions to mitigate disasters, the warnings alone won’t provide much of a stop gap.
Setting an example in risk management
IBM provides a great example of how companies can use this sort of technology to prevent costly disruptions in their supply chains.
With IBM’s huge global outsourcing budget totaling tens of billions of dollars, including 20,000 suppliers, its supply chain is understandably complex, especially since some suppliers are, by necessity, sole source suppliers.
Executing a global sourcing strategy, where sourcing is conducted across developing countries, has a cumulative effect on the amount of risk introduced into the supply chain.
To manage risk, the company’s global sourcing looks far beyond unit cost to the total cost picture. All dependencies are fully mapped, and wherever possible back up sources are identified along with their impact on the company’s supply chain.
The company also develops contingency plans for events that will eventually happen in the future (e.g. an earthquake or pandemic).
In March 2011, the Japanese tsunami and earthquake placed IBM’s Total Risk Analysis tool front and center, and it responded flawlessly. Within a few hours, IBM determined all its potential supplier problems, immediately assembled details and developed backup plans.
IBM’s recent purchase of the Weather Channel has added a myriad of predictive analytical capabilities to its arsenal. It has also added the resources of its Watson supercomputer.
The utilization of earthquake early warning technology is one more resource in its comprehensive portfolio dedicated to managing all manageable components of its intricate supply chain.
What is your company doing to identify and prevent major disruptions in your supply chains?
disqus comments